For many years, the use of robots in production was an image you encountered in particular in the automotive industry. Behind high fences, giant robot arms assembled heavy bodyparts. But robots have changed and they perform a very wide range of tasks these days. A flexible collaboration between humans and robots is the culmination of this - no fences, no pre-programmed sequences, yet nevertheless safe. Fanny Platbrood, Head of Strategic Product Management for Safety Systems and Services explains what is required for this.
”The holy grail of human-robot collaboration”
Robots have been driving industrial automation forwards for several decades now: “While they were predominantly used in the 1970s for handling heavy loads, we have observed a remarkable development over time. Robots have become smaller, more maneuverable, more flexible and can perform tasks at high rates. This has expanded their fields of application enormously,” says Fanny Platbrood and adds: “Robots can be found in nearly every industry these days. Especially where precision is required, for example in the electronics industry where ultrasmall components are processed.”
Collaborative robots are creating new possibilities
When the first collaborative robot came on the market in 2008, it opened up a completely new dimension in the collaboration of humans and machines. Platbrood recounts this enthusiastically and remembers: “That was a groundbreaking innovation. Firstly, because collaborative robots are truly able to work with and around humans. And secondly, because they became a lot easier to operate. The programming of robots is now similar to the use of apps on a smartphone. You don't necessarily need to be a technical specialist to program a robot these days. This lowers one of the biggest hurdles to the use of robots.” Although fences are becoming less and less desirable when collaborating with lightweight robots, safety continues to remain an important issue. An effective protection of robot applications, particularly collaborative ones, should not scare people off, but rather create trust. The person interacting with the robot should have no concerns about their safety. A risk assessment right at the beginning is therefore essential. “We need to consider the entire system when doing so, right through to the end effector and the object it is transporting. If, for example, the robot is carrying something with a sharp edge and the end of the robot arm is not adequately protected, this can lead to irreversible injuries. The prerequisite for a ‘trusting’ collaboration is a risk assessment and the risk reduction measures derived from it,” says Fanny Platbrood and adds: “A requirement for collaborative robot applications is that they have a smart means of protecting the end effector in order to greatly minimize the risk of injury. That would be an absolute game changer because it would allow many further collaborative applications.”
Safety increases productivity
But when we also take a look at the entire work situation, we see potential for optimization. In human-robot collaboration, it is necessary to continuously monitor speeds: When a person approaches the robot, it needs to reduce its speed, perhaps even come to a complete stop. The most common solutions these days are based on safety laser scanners. Programming the protective fields can, however, become technically complex as the number of fields increases and doesn't provide any flexibility in implementation. The product manager believes that 3D safety cameras could offer a solution approach for monitoring the entire robot application and thereby continuously recording the movements. “In the end, the solution will probably involve a combination of different technologies in a system that is easy to integrate and configure. If we succeed with this step, there will be no pre-programmed workflows for robots, instead they will make decisions independently based on the environment and requirements”, she says.
Fanny Platbrood is convinced that this development is not too far away and adds a further aspect that has already fundamentally changed the way we collaborate with robots and will continue to change it: “Digitalization allows much more dynamic developments. We will then no longer be talking about robot applications, the productivity of which we can increase through safe flexible workflows, but rather about a complete network of collaborative and stationary robots, where AGVs, AMRs and humans work together in an overall system. The transmission of data between machines would then allow self-determined workflows appropriate to the situation. Safety in this context no longer means having to accept the trade off of slower processes because, for example, this creates wait times. No, it’s safety that actually makes all of this collaboration possible. And that for me is the holy grail of human-robot collaboration: Creating Safe Productivity - We want to increase the productivity of our customers through safe, efficient processes.”
More articles
Safety for collaborative robot applications
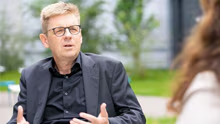
Globalization in companies: Being independent together

“Digital first” alone does not yet create any added value