The digital revolution is in full swing. And it’s no wonder: Having an automated process structure – something from which even manual processes benefit – means not only significant cost savings, but also increased productivity and improved transparency. It’s an attractive prospect for many industry players – including the JentnerGroup. When looking for an opportunity to automate their workflows while simultaneously tracking all the associated processes, the company came across the Tag-LOC System from SICK. The system was specially developed for locating and tracking material, load carrier, and industrial vehicles in real time.
Automation in electroplating: more efficient product controlling thanks to location-based solution from SICK
RFID technology as the first step
The JentnerGroup, located in Pforzheim, Germany, is a leading provider in the field of subcontracted electroplating and metal finishing. In order to retain their position, the company is breaking new ground in electroplate finishing. In the first step toward complete automation, the existing operating data acquisition system was supplemented by RFID technology (Radio Frequency Identification) in summer 2019 – this was the first milestone.
UWB technology as the logical next step
Though this already achieved a great deal, the company wanted the additional option of plant-wide real-time localization with positioning accuracy in the decimeter range. Because this is where RFID technology reaches its limit, they changed over to UWB sensor technology (ultra-wideband) in the form of the Tag-LOC System from SICK in 2022.
Interplay between the Tag-LOC System and Asset Analytics
The JentnerGroup initially used the system from SICK in barrel plating. The antennas positioned above the electroplating lines receive signals from the tags on the electroplating barrels. The time stamps are transmitted to the Asset Analytics software platform, making it possible to automatically identify all production parts, and to calculate and track their position during the entire, multi-step electroplating process. Asset Analytics can also be used to record sensor-based data by connecting RFID or barcode systems and process it into process-relevant information.
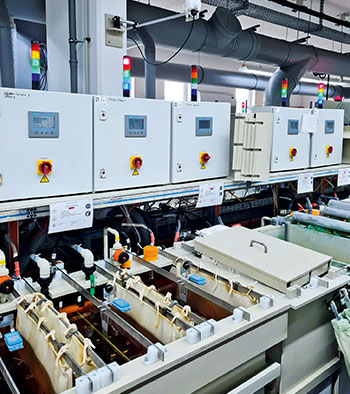
This allows the JentnerGroup to benefit from comprehensive data on the flow of material based on technology-independent software, and to keep an eye on everything via a central user interface. In concrete terms, this means that as soon as a barrel or rack of goods with a uniquely identifiable UWB tag enters or leaves the area above an electrolyte or wash basin, the Tag-LOC System will recognize this action using the position data and send an appropriate event message to the JSPS (Jentner Smart Plating System, previously BDE) that was developed in-house. Depending on the surface and the desired layer thickness, this intelligent system calculates the specific adjustment values for each article and transmits them to the rectifier, whereupon the electroplating process will start automatically. It is no longer necessary to manually intervene, and all the important data is saved and prepared for possible analyses. Connecting Asset Analytics to the JSPS didn’t require any effort to develop either, because everything was conveniently managed via individually configurable JSON webhooks. This allows user-specific information for the enter and exit events to be sent to and received from any http-capable remote station.
Robert Schröder, Product Manager Location Solutions at SICK, who accompanied the project as a consultant, summarizes: “Knowing where each part of the goods is within the workflow at any time enables the customer to carry out predictive processing with forecasts on the predicted delivery quantities and times that are constantly updated.”
One manufacturer – many possibilities
This lays the foundation for more efficient product controlling. All information and specifics relevant to the electroplating step are transmitted to a digital production record. In addition to accuracy and range, flexibility is also improved compared to the previous system, while high energy consumption and interference with other radio systems are a thing of the past. The SICK offering also comprises even more products that can be utilized in other areas, such as receiving goods, intermediate storage, and picking. The JentnerGroup doesn’t want to pass this opportunity by, and has implemented additional SICK solutions alongside the Tag-LOC System: With the Visionary-T 3D snapshot camera, requests can be made in the area of logistics to check whether the goods have arrived and are in the designated pallet location. The corresponding information is also sent to Asset Analytics, and is processed further and visualized together with the position data so that staff are always up to date. In addition, individual notifications on the pending receipt of goods can be sent by webhook or other channels (e.g. via e-mail or Teams). For the automated handling of medical instruments using a cobot in a test cell, the InspectorP63x 2D vision camera is being utilized as part of the Prometheus project to detect anomalies on coated medical tools.
The next steps
As part of their digital transformation, the JentnerGroup is also implementing this digitalization concept together with SICK at their new site, which was recently put into operation. Modern digital rectifier technology is being used on 4,000 square meters of production space for pure, high-quality manual electroplating. Here, the Tag-LOC System solution comprises 26 antennas that monitor 104 baths, two driers, eight assembly workstations and four temporary storage areas for raw and production material.
Summing up, Marcel Scheidig, Head of Technology at the JentnerGroup, says: “With our new production hall and the wide range of possible applications of the Tag-LOC System in combination with the 3D camera for automating the detection of incoming goods and the AI camera for our cobot from SICK, we are now perfectly positioned. We have completely interconnected our data streams so that we can provide our customers with a comprehensive, transparent digital production record with all the relevant influencing variables and parameters for each of their hand-coated workpieces, and also provide them with the CO2 footprint of their coating.”