Process quality tripled, process speed doubled – this is how the Swiss company Steinemann DPE summarizes the outcome of using the SPEETEC non-contact speed and length measurement system. Steinemann DPE, which is a subsidiary of the German company Leonhard KURZ Stiftung & Co. KG, develops and manufactures in Switzerland digital print finishing systems (digital lacquering and digital metalization) using UV inkjet technology and uses SPEETEC sensors for these. The measurement data collected at high web speeds and with µm accuracy enable the print heads to be controlled with great precision. This considerably improves the high-quality appearance of the digitally finished packaging and print products, speeds up the digital lacquering and metalization processes, and opens up new finishing possibilities.
Print finishing: increase in quality through non-contact speed measurement
Slip-free, without measuring elements or marks, with no damage to sensitive surfaces, and with no wear of tactile measuring elements, the SPEETEC laser surface sensor can measure a wide variety of web and continuous materials as well as blanks with maximum precision and stability. “A peak through a thread counter, a type of measuring magnifier, provides a significant argument in favor of SPEETEC: the high registration accuracy of the digital lacquering or digital metalization,” explains David Gräub, Project Manager & Engineer Inkjet at Steinemann DPE AG in St. Gallen, Switzerland. “In contrast to the traditional encoder solutions, we were able to improve the registration tolerance from ± 0.3 mm to ± 0.1 mm, i.e. by a factor of 3, using the slip-free measurement sensor. The means that we can apply digital finishing touches, for example fine metalized lettering or thin lacquered lines, exactly where they need to be with maximum precision and without registration errors. This gives the already high-quality offset and digital print products an even more refined appearance.”
Print finishing: from high quality to refined
With its innovative DM-Maxliner and DM-Uniliner series of lacquering systems for digital spot and relief lacquering and digital metalization, the Swiss company Steinemann DPE AG is one of the internationally leading print finishing specialists in the graphics industry. The company, which is a subsidiary of the German company Leonhard KURZ Stiftung & Co. KG, develops and manufactures in Switzerland digital print finishing systems (digital lacquering and digital metalization) using UV inkjet technology and uses SPEETEC sensors for these. The digital finishing is performed in a wide variety of ways: flat or embossed lacquer and metalization effects, ultra-fine lacquer and metalization structures, a variety of stroke widths, perfect gloss even with thin lacquer layers.
Whether partial or full-surface, whether for envelopes, labels, brochures, posters, packaging or other print products: The digital print finishing systems from STEINEMANN DPE stand for maximum quality, performance and value for money. Machines like the DM-Maxliner, in which the non-contact SPEETEC measurement system is used, can process up to 10,000 sheets per hour at speeds of up to 100 m per minute – and at a resolution of 600 dpi. “The accuracy at which we can measure the speed of the vacuum belt with the 1 m x 0.7 m sized sheets is crucially important for the quality of the digital print finishing,” says David Gräub.
One approach to increasing the quality of the digital finishing was therefore to increase the accuracy at which the speed of the vacuum belt is measured. The previously used measuring wheel encoder solution was affected by factors such as variations in thickness due to contamination, slip, moisture formation and abrasion. “Thickness variations, for example, caused peaks in the encoder signal and thus register inaccuracies that were visible in the thread counter,” explains David Gräub. “By switching to the SPEETEC, these and other influencing factors no longer play a role,” confirms David Gräub.
SPEETEC improves the quality and possibilities of print finishing
The SPEETEC was specially developed to measure sensitive materials like those at Steinemann DPE in a non-contact manner. Problems due to extremely smooth and slip-prone materials, highly sensitive surfaces such as decorative prints, or materials that can affect the measuring wheel through wear, adhesion or abrasion simply do not occur with this measurement sensor. Furthermore, switching from a tactile encoder to the non-contact measurement system is easy to do because it also comes with the familiar TTL or HTL interfaces included with incremental encoders. Compared to expensive laser velocimeters, the sensor offers the advantage of operating with a class 1 laser – which requires no special protective measures – rather than the class 3 laser light used in velocimeters.
In the application at Steinemann DPE, the SPEETEC measures the speed of the perforated rubber vacuum belt on which the sheets are transported through the machine at a separation of 150 mm. The measurement system is installed directly behind an image processing system that detects the position of the sheet in the x and y direction as well as a possible slight rotation on the belt. In addition, it detects any possible local deformations due to moisture or storage, for example at the corners of the sheet. This information is taken into consideration in the printer controller and combined with the measurement data from the SPEETEC. This enables the print heads in the printing tower to be moved to the right location with maximum precision. “Besides increasing the quality of the print finishing, the measurement accuracy of the SPEETEC allows us to double the belt speed without compromising on quality and thereby process orders significantly faster.
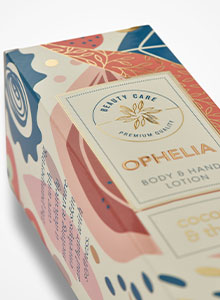
Added to this, we can now implement even more special effects, even more filigree structures and elements as well as smaller font sizes,” explains David Gräub. The threefold reduction in the registration tolerance is of particular advantage when a sheet passes through the machine twice for different finishing steps. "We can now solve this demanding task for often especially high value materials with maximum precision and reliability," says David Gräub.
The SPEETEC is a motion control sensor for linear movements which, thanks to its combination of non-contact and slip-free measurement principle as well as versatile performance and easy integration, enables the quality of products and processes to be significantly improved. This is impressively demonstrated by its use in the digital print finishing machines of Steinemann DPE.
Pace: Magazine from the 2023 Annual Report
The highly dynamic nature of the markets and technological progress require solutions to be found at an accelerated pace. We are constantly adapting our speed in order to gain and maintain a competitive edge by using our accelerating powers sensibly.
The articles in the magazine show that those who gain a head start and time through speed can use it intelligently for new ideas and sustainable decisions.