Whenever metallic objects need to be detected without contact, inductive sensors are ideally suited for this purpose due to their electromagnetic operating principle. In addition, object detection is contactless and the initiators contain no moving parts. This, together with the special ASIC technology and special manufacturing processes, e.g. chip size packaging technology (CSP) and elastic hot-melt encapsulation to protect the components, make inductive sensors particularly robust and durable.
Inductive sensors - Function, mounting and application
Functionality inductive sensors
Due to their functional principle, inductive sensors can detect not only magnetic but also electrically conductive materials, aluminium, brass, copper and stainless steel. The best results = highest sensing distance are produced with ferromagnetic metal. The ferromagnetic metal is also used as a reference value for the nominal sensing distance Sn in the data sheet. Other metals have a smaller sensing distance, which can be calculated using reduction factors.
If there is no detectable target in front of the sensor, it is not influenced = attenuated.
Sensing distances
The nominal sensing distance (Sn) given in the datasheet is based on an object to be detected made of steel (St37) with a square shape and a thickness of 1 mm. The minimum size of the target depends on the sensor itself and is defined as the diameter of the active area of the sensor or 3 times the nominal sensing distance, whichever is greater. The nominal sensing distance Sn does not take into account voltage and temperature variations or manufacturing tolerances. The effective sensing distance (Sr) takes into account manufacturing tolerances and the usable sensing distance (Su) takes into account voltage and temperature variations. The most relevant sensing distance for the user is the secured sensing distance Sa, in which all tolerances and fluctuations are taken into account.
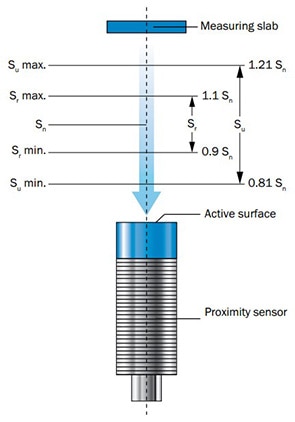
- Nominal sensing distance Sn: No consideration of manufacturing tolerances and external influences such as temperature, etc.
- Effective sensing distance Sr: 0,9 Sn < Sr < 1,1 Sn (at 23 +/- 5 °C Manufacturing tolerance)
- Usable sensing distance Su: 0,9 Sn < Su < 1,1 Sn (entire temperature and voltage range)
- Secured sensing distance Sa: 0 < Sa < 0,81 Sn
Correct switching at different temperatures can only be guaranteed within the secured sensing distance Sa.
This formula can be used to calculate the respective operating sensing distance (Sa) for different materials. The calculated value "Sa" ensures the function within the temperature and voltage range as well as the manufacturing tolerances.
Sa = Sn x 0,81 x R
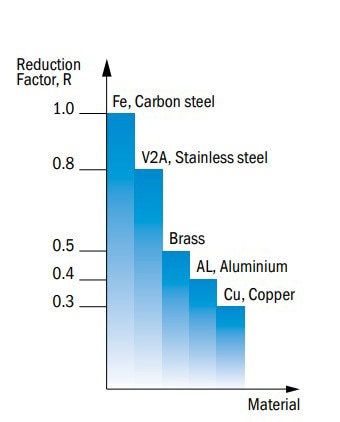
Reduction factor R
The material of the object to be detected is decisive for the detection capability of the sensor. The highest sensing distance is provided by an object made of steel, which is also used to specify the nominal sensing distance. To obtain a sensing distance for other materials, a reduction factor (R) is used.
The reduction factor (R) indicates the change in sensing range which is caused by a different material compared to the stnadard target (zinc plated steel).
The reduction factor is determined by two properties:
- Conductivity of the target material (weak effect)
- Permeability of the target material (strong effect)
Installation of inductive sensors
When mounting inductive sensors, the two main types - flush and non-flush - are named.
In the non-flush version, the ferrite core with coil is not enclosed by a metal housing. This means that the magnetic field generated is not blocked by the housing, resulting in a larger field and thus a greater sensing distance can be achieved. Non-flush sensors can only be mounted flush in non-conductive material.
Flush sensors have a metal ring around the sensor head, which protects the sensor from influences by the surrounding material. Due to this shielding, the electromagnetic field is a bit smaller and the sensing distance is therefore shorter. Flush sensors can also be installed in a non-flush manner. In this case, however, the reduced sensing distance due to the lack of surrounding material must be taken into account.
Mutual influence
In general, inductive sensors influence each other. To prevent this, certain distances must be maintained. Since the electromagnetic field generated by non-flush sensors is greater than that of flush sensors, non-flush sensors require a greater distance from each other. The distance between flush sensors should be at least one times their diameter and the distance between non-flush sensors two times their diameter. If the sensors have different vibration frequencies, they can be installed closer together. This must be clarified in each individual case.
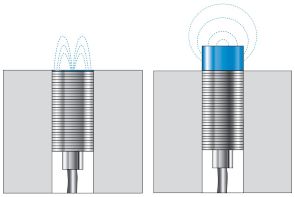
Use and application of inductive sensors
Standard applications in industrial environments are defined by moderate requirements, e.g. IP67, no permanent exposure to oils and coolants or a "normal" temperature resistance. The IME series is suitable for these operating conditions, as it offers the best price/performance ratio for applications in standard industrial environments. A standard application for this would be the positioning of a workpiece carrier. The IME inductive sensor detects the presence of the metallic workpiece carrier and its trigger signal is used to control and trigger the stop cylinder at the respective assembly station. When detecting metal objects (e.g. metallic workpiece carriers) at close range, inductive proximity sensors are the most reliable and economical solution compared to other sensor principles.
If the environmental conditions become more demanding, different performance features are required depending on the application. E.g. increased temperature resistance, chemical resistance, leak tightness, shock, vibration and outdoor resistance, or additional intelligent functions. While these special requirements have so far often been met by appropriately designed special sensors, the IMB product family offers an "all-rounder" that combines the individual strengths of the "specialists" in one universal sensor. The sensors in corrosion-resistant stainless steel housings are available in M8 to M30 designs and are specified, among other things, for a temperature range of -40 °C to +100 °C, for permanent splash or immersion contact with water, tightening torques of up to 100 Nm, shock and vibration resistance of up to 150 g, or for permanent contact with aggressive cutting oils and cooling lubricants. As a product family, the IMBs thus meet essential requirements for robust, inductive sensor technology, such as is used on container spreaders, in car washes, in machine tool construction or on gates and barriers in outdoor applications. The universal application versatility of the IMB enables users - usually machine builders from these industries - to significantly reduce their type diversity - which makes their entire procurement, engineering, logistics and service processes much more efficient.
Machine tools can be mentioned here as an example of use. They require different tools depending on the machining process. To avoid interruptions due to tool changes, several tools are clamped in a rotatable tool turret. After each step, the tool turret is rotated into the working plane so that the tool suitable for the next step, can be used. The sensor thereby takes over the control of the correct position of the tool turret. The IMB inductive sensor is specially designed for such environments. It is insensitive to oils and cooling lubricants and has a sealing concept with protection class IP 69K.
Technically as well as economically, the IMB is positioned between the various standard inductive series as well as the ultra-robust IMF product family.
These are also stainless steel sensors in designs M8 to M30 for flush and non-flush installation and for working distances between 2 mm and 20 mm. In accordance with their main area of application - machines and systems for the production and packaging or filling of foodstuffs - IMF sensors in protection classes IP 68 and IP 69K, among others, impress with their special tightness, which is particularly important in the frequent high-pressure cleaning of systems in the food & beverage sector. The materials used - including stainless steel 1.4404 / AISI 316L and the liquid crystal polymer LCP - are FDA-compliant. The stainless steel of the Ecolab-certified inductive sensors also exhibits excellent resistance to chlorine-containing media, such as hypochlorite-based disinfectants or chlor-alkaline foam cleaners. For all their robustness, the IMF sensors also offer high accuracies, short response times, and easy commissioning and remote diagnostics.
Smart Sensors - Suppliers of information for industry 4.0
Neither the IMB nor the IMF need do without a "smart" inner life, i.e. intelligent basic functions. The special ASIC in the sensors is not only responsible for the high-precision setting of the operating distances and temperature compensation, but also - as an option - for the communication capability via IO-Link. In addition to reporting the switching status, this interface can be used, for example, to verify the secured sensing distance, to carry out basic function diagnostics as part of condition monitoring, or to set, activate or change parameters such as the switching or counting function.
I want to stay up to date and regularly be informed about new articles!