Velux is renowned for high-quality windows and the accessories that go along with them. Dedicated to always finding the best solution, the software department developed software that the company uses to automate production and quality control. Velux has also been using machine vision technology to make manufacturing and assembly processes more efficient – and now they are getting an even greater efficiency boost through Artificial Intelligence and Deep Learning from SICK.
Deep Learning and machine vision technology improve production efficiency at Velux
Lasse is a senior automation programmer at Velux A/S and a leading person in the team for the development of machine vision solutions. A passionate and very versatile programmer, Lasse can attest to the fact that developing a rule-based software for machine vision solutions is often a time-consuming process.
Deep Learning – human-like intelligence
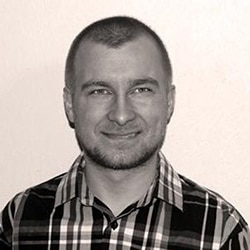
When Lasse heard about SICK’s Deep Learning solutions, he saw an opportunity to improve efficiency and make better use of the company’s skilled employees by sparing them from carrying out the more monotonous work tasks.
Deep Learning is subset of Artificial Intelligence based on neural networks, which mimic the human way of seeing, perceiving, and deciding. In recent years, this technology has become much simpler to use and it no longer requires the heavy computer infrastructure that made these solutions unattainable for many organizations in the past. Today, Deep Learning solutions can be run on compact industrial controllers, making it more accessible and relevant for industrial use.
From 200 to 20 person hours
In the past, Velux Danmark A/S has ensured product quality by carrying out manual inspections of the sub-components for their windows. While this system has always worked well, there are clear limitations. Depending on how experienced the employees are, there could be small variations in the assessment of the components. The need to work quickly and conduct the same assessment all day long also carries the risk of employees becoming “speed blind”. Aware of these limitations, Lasse Hedeby decided to introduce camera inspection to support the operators as they carry out this manual work.
That leaves Lasse with a huge workload, though. Velux A/S has many sub-processes. Each one of these requires the development of new software for new machine vision systems. Putting together a rule-based software for each process can easily take up to 200 person-hours. Using the Deep Learning solution that draws on SICK AppSpace significantly reduced the need to code, which meant that Lasse was able to reduce the time to develop new software to a fraction of the time (20 hours).
One of his most recent projects used intelligent solutions from SICK to check that aluminum profiles, a sub-component of a window blind, are sufficiently filled with polyethylene foam. This can be tricky, because the way the foam expands when it is sprayed into the profile is not uniform. That means that there is not a clear yes or no when evaluating the filling process.
Solving problems through close cooperation
Training the software to recognize perfectly filled profiles went quickly and delivered good results, but the process was not perfect. The profiles are long and thin so that when the cameras check the profiles, the relevant information for the evaluation only takes up a very small part of the image. The solution required the adaptation of a standard SensorApp, dividing the image from the machine vision sensor from SICK into three separate images, to make the Deep Learning algorithm more efficient.
The software engineers of Velux A/S and SICK A/S supported each other in the development of the solution, and both teams benefited from the experience. Lasse Hedeby said that he had “never before experienced a supplier who is so flexible and provides such good support as SICK.” Conversely, the team at SICK is pleased to work with such a serious partner and to have a satisfied customer.
The way forward for industrial automation
Lasse is already working on the next task, where AI will be used to ensure that screws in a bracket are mounted and tightened. The task can be complex to solve with ordinary rule-based machine vision, as both metal and screws can have a very diverse surface with lots of light reflection. However, initial indications are very promising. The ability of the SICK Deep Learning solution to easily handle such a diversity of complex problems clearly shows that this is the way forward for camera-based inspection and industrial automation.
Read more
Intelligent Inspection SensorApp: Makes Deep Learning accessible
Every movement in sight: The camera-monitored assembly facility at RIBE Anlagentechnik
For Increased Efficiency, Deep Learning is the Future
2D- och 3D-bildbearbetning konfigureras individuellt och enkelt – tack vare SICK AppSpace