In just six months, Liebherr-Transportation Systems completely reconstructed two manufacturing lines after a fire at its Tsarimir location in Bulgaria. The lines were also significantly upgraded. From planning right through to system construction, the company took advantage of the know-how of Liebherr-Transportation Systems in Austria and the safety expertise of SICK Austria.
Next generation air conditioner manufacturing
Liebherr-Transportation Systems, which is headquartered in Korneuburg in Lower Austria, is known internationally for its technical solutions in the area of air conditioning technology, hydraulic actuation systems, and its electronic components for all types of rail vehicles. The series production of air conditioning systems for rail transport and trailer cooling is currently located at their Tsaratsovo location in Bulgaria. In 2019, several production lines in their manufacturing facility in Tsarimir were destroyed at the same time by a fire – a big challenge for the company.
From Korneuburg to Bulgaria
Liebherr approached the reconstruction offensively and used the opportunity to bring the systems up to the state of the art and thereby raise them to a new technical level. Liebherr-Transportation Systems in Korneuburg was responsible for implementing and installing the new production lines. Abu Hurayra Bin Ahmad, Department Head Industrialization at Liebherr-Transportation Systems: “We not only produce, deliver and maintain air conditioning and hydraulic systems, we also construct the machines used to manufacture them – one of our specialist areas at the Korneuburg location.”
Two out of three assembly lines destroyed
Due to its size and complexity, the production in Tsarimir was divided into three assembly lines – this division was also retained in the newly constructed facility. Roland Wolf, Industrial Engineer at Liebherr-Transportation Systems: “On one line we manufacture the E-Box of the air conditioners, which houses the electrical connections as well as the controller and regulator. This less complex area was able to be reconstructed using the equipment available on site in Tsaratsovo. Line 2 – on which the cooling modules are produced – and line 3 – on which the entire system is assembled – where hit very hard, however.”
“The facility was divided into these three manufacturing lines because the three areas require very different manufacturing steps, and need to handle components of differing sizes,” adds Abu Hurayra Bin Ahmad.
Phoenix from the ashes – using new technologies
“The fire was a catastrophe, but also gave us the opportunity to implement a wide variety of new concepts – and very quickly as well.” The requirement was for both lines to be re-established within just six months. “We managed to construct the lot in just three months and three weeks, and needed two months and three weeks for design and purchasing – it was an extremely demanding project plan but we achieved it,” explains the department head Ahmad proudly.
The manufacturing lines – apart from the E-Box manufacturing – were first set up and tested in Korneuburg. What was especially pleasing to the two responsible persons in Korneuburg was the fact that many previously absent technologies were being used. A Kanban material delivery system and semi-automatic test steps were developed, the manufacturing became paperless, and the issue of safety gained an entirely new importance as it was able to be completely revisited.
Machine safety of great importance
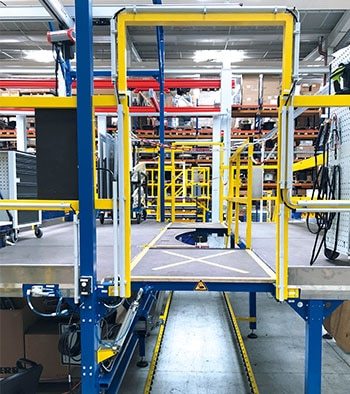
“From very early on we saw that great importance would be placed on the safety of the machinery on these lines. Heavy parts weighing up to a tonne move along the line and there are machine and transport elements that are constantly in motion. Safety was therefore a key issue for which we wanted to have true specialists on board,” says Roland Wolf. The collaboration with SICK opened up the possibility of getting assistance with all matters of machine safety from A to Z. Or better said R to V, because SICK offers services from risk assessment right through to verification and validation, and thus everything to do with safety, all from a single source.
Five steps to a safe machine
The risk assessment is the first step on the path to a safe machine. Martin Wimmer, a certified expert for machine safety at SICK Austria says regarding this: “The Liebherr team got us involved very early when developing the manufacturing line – that saves time, money and planning effort. We first evaluated the risks using the 3D models provided by the Liebherr team. Based on this evaluation, we produced a safety concept to adequately minimize the risks. Step three was the hardware and software design, i.e. the technical realization of the measures. The solutions were then implemented, including support during commissioning. The fifth and final step was the verification and validation of the system in Korneuburg.“
Plan changes can result in risks
Before the fire, the facility in Tsarimir was built on platforms. For the new facility, it was decided to use a concept with conveyor belts – an important point when it comes to safety. Abu Hurayra Bin Ahmad says regarding this: “In the case of the cooling module line, this was relatively manageable – on the final assembly line however, for which my colleague Roland Wolf was responsible, this gave rise to many safety related issues.“ That is also challenging in terms of costs, because every plan change can result in new risks and thereby new machine design-related measures, additional costs, or perhaps even further plan changes if it turns out that there are better solutions. “That required close teamwork with SICK,” says Roland Wolf.
Pneumatic transport bridges
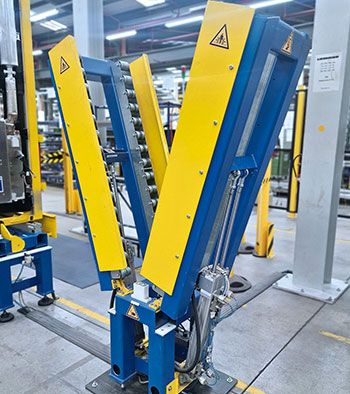
A particular risk in the final assembly area was the pneumatically moving bridges that were used to open and close the belt conveyors. Each workstation is connected to the next one by such a bridge. When they are closed, the heavy parts can be conveyed from station to station. The pneumatics used here harbors particular risks. The bridges were a good solution, however, for utilizing the available space as best as possible. Roland Wolf adds: “It was necessary to ensure that assembly work on the product and also the material flow was possible from the front and from the back. We therefore needed 360-degree accessibility, including for products that could be up to three meters tall and required work on two levels. We therefore decided for pneumatic transport bridges.”
Doubly secured
Once a manufacturing step is completed, the employees exit the area. Two people then actuate safety switches and the bridges are lowered so the air conditioning units can be transported onwards. The bridges then move up again and the next cycle begins. To ensure the safety of the workers in the vicinity of the heavy bridges, all areas are doubly secured because nothing must be allowed to happen to the workers if, for example, a pneumatic hose breaks, a cylinder is blocked, or the air is suddenly lost.
High voltage test of the air conditioning units
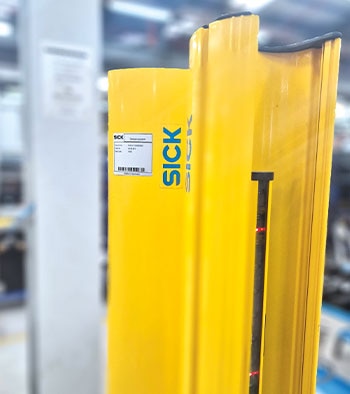
Another important aspect in terms of safety was the testing of the units. Roland Wolf says: “If we were to fully assembly the air conditioners, we would not be able to perform detailed testing on them. We would have to unplug and disassembly everything again. We therefore needed to implement a high voltage test in the middle of the production line, and another at the end of the cooling module and refrigeration unit lines. These had to be segregated off. The safety light curtains used for this are almost two meters high.” The protection zone for the bridges is over 25 meters long. The final assembly of the refrigeration units also harbors specific risks, for example a fall risk if no unit is present. A flap therefore surrounds the equipment to protect the employees from this hazardous area. Abu Hurayra Bin Ahmad: “This flap is a safety feature, but itself poses a crush risk. It therefore had to be suitably protected. There is also an earth measurement at this station that had to be protected as well.”
Safety with the right timing
Each refrigeration unit that Liebherr manufactures for trailer cooling contains three cooling modules. Everything must therefore be perfectly timed to ensure the ready-to-install modules are available at the right time. This includes pressure tests on the cooling module line, because every cooling circuit must be tested at 38 to 40 bar – including safety devices. Abu Hurayra Bin Ahmad: “We are very pleased to have been able to rely here as well on the expertise and safety technology from SICK.”
Many safety solutions in use
The new production lines use, among other things, the intelligent deTec safety light curtains, TR110 Lock safety switches with locking function, various safety command devices (like emergency stop, reset, and enabling switches), signal lamps, various safety switches, and the versatile, programmable Flexi Soft safety controller. Sometimes, as well as having the right technology you also need to think outside the box. For example the feeding of the refrigeration unit in final assembly, where you need to ensure that a unit is actually present at the station. This safety feature was implemented using the Safeguard Detector developed by SICK, which is otherwise often used in the packaging industry to monitor the feed opening for unfolded cardboard boxes.