DS Smith, a worldwide leading provider of sustainable packaging solutions, paper products and recycling services, needed to upgrade an end-of-line monitoring solution to automate a labor-intensive process, by replacing it with one that provides higher precision, real-time measurement capabilities. They turned to a solution based on SICK’s sensor intelligence, Microsoft Azure Depth Platform and AI software developed by Neadvance.
DS Smith, a leading sustainable packaging manufacturer pilots digital 3D dimensioning to transform logistic operations
DS Smith is a leading provider of sustainable fibre-based packaging that improves transport and storage efficiency, boosts retail presentation and increases product sales for their customers worldwide. Headquartered in London, the company plays a central role in the value chain across sectors including e-commerce, fast moving consumer goods and industrials and is constantly looking for ways to improve its production process. To optimize warehousing processes, the availability of real-time dimensional data of packaged product is essential.
The challenge: Measuring dimension, volume and number of palleted packaging products
DS Smith creates packaging solutions that meet their customers’ supply chain requirements and improve the end-customer and brand experiences with customed made packaging. This puts a major challenge to DS Smith as they need to design, handle manage and ship a large variety of custom packages to various end-customer locations and warehouses. At the end of the packaging production process known as the end-of-line, it is crucial to precisely determine the output of the production line by measuring the dimensions, volume and number of palleted packaging products. Dimensional and quantity data is the key to customize and optimize warehouse and freight processes and ensure the most efficient use of available space.
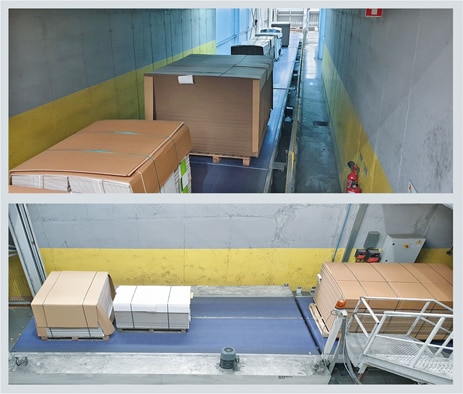
The solution: digital end-of-line monitoring
As a part of their digital transformation, DS Smith wanted a digital end-of-line monitoring solution that would integrate with their current production processes and provide more accurate dimensional data. They turned to Neadvance, a computer vision and artificial intelligence solutions provider for industry and SICK, a leading producer of sensors and sensor solutions for industrial automation applications, to help them address their challenge and implement a pilot solution, in order to validate the results and confirm the potential for future improvements. Using SICK’s Visionary-T Mini based on Microsoft 3D Time of Flight (ToF) technology, DS Smith was able to capture the necessary data quickly and accurately without adding resources or interrupting production. Solution integration and 3D vision camera processing was designed by Neadvance.
The Visionary-T Mini uses the innovative 3D time-of-flight camera technology by Microsoft with depth data that allows fast and accurate measurement of the spatial dimensions of pallets and their volumetric load. Mounted above the end of the production conveyor belt, just before the pickup point by a forklift, the Visionary-T Mini solution can be incorporated without major integration effort. Despite the small camera size, SICK has designed a robust 3D ToF snapshot camera for industrial use that operates at high availability 24/7. The compact device with a protection rating of IP67 provides calibrated high-quality 3D depth data and 2D intensity data for further external data processing. “With 3D snapshot camera technology such as 3D ToF, Visionary-T Mini is able to create three-dimensional images of a scene without any moving parts in the device or movement of the sensor itself”, says Dr. Anatoly Sherman, Head of Business Unit 3D Compact Systems at SICK. Since the distance data for each pixel of the complete sensor resolution is calculated very quickly at a high repetition rate, the occurrence of blurring effects and motion blur can be prevented successfully. The Visionary-T Mini is currently on the verge of a broad market launch. Visionary-T Mini CX is the first product in a series of SICK products based on Microsoft ToF technology, which showcases a long strategic collaboration between SICK and Microsoft.
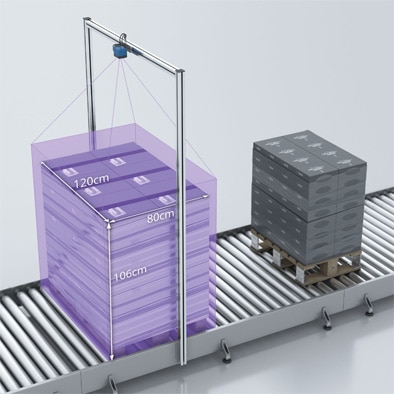
Intelligent image processing combining 3D and 2D data
DS Smith’s well-established production process is thus not disturbed nor changed, the dimensions of the produced goods are instantly captured and the volume is calculated using Neadvance Edge software. “The intelligent image processing with the capability of combining the 3D and 2D data is the key to solve the application in a reliable way”, says Jose Pedro Ferreira, Head of Business Development & Sales at Neadvance. In addition, the Visionary-T Mini 2D image data is used for subsequent quality monitoring and plausibility checks in the event of error or process analytics.
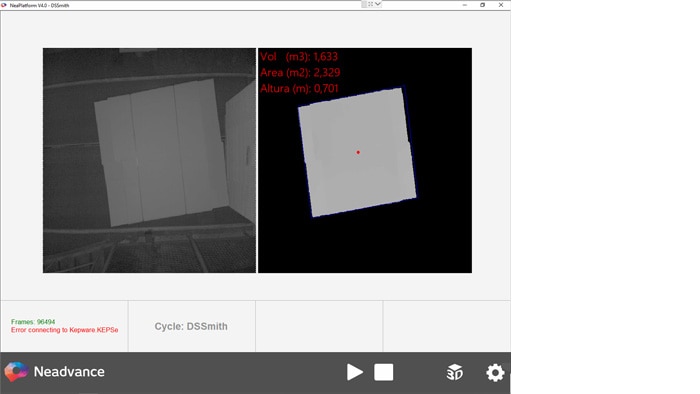
DS Smith’s 2D and 3D data is pre-processed at the Edge, filtered, and persistently stored on SICK’s digital service. The sensor system communicates with the digital service via Microsoft’s Azure IoT Hub which encrypts the data connection. “SICK developed the digital solution based on the versatile Azure web services. DS Smith can access this Software-as-a-Service via the Digital Service Catalog of the SICK IntegrationSpace. SICK’s cloud software experts tailored this solution and operate the digital service individually for DS Smith. Our customers can be focused on their core business while making use of SICK’s digital services.” explains Alexander Wiestler, Head of Global Product Management Industrial Integration Space at SICK. The SICK Dashboard provides DS Smith with the number of pallets per hour and the manufactured production volume in real-time. In turn, data storage and analysis in the Azure cloud captures current data and can compare it with historical data in real time from any terminal device. Using this set of data, scaled to a full implementation, production employees, system engineers, and production managers will then have new possibilities to optimize production based on intelligent insights. With automated data and image upload to Azure, DS Smith can access its material flow information 24/7, regardless of location.
A system with far-reaching possibilities for more efficient logistics
At DS Smith Esmoriz site (near Porto), Neadvance, SICK and Microsoft provide the reliable data that is needed to solve a crucial task on the shop floor and makes logistics more efficient. Azure services expand opportunities for DS Smith to analyze and optimize processes sustainably. The solution combines on-site machine vision with cloud processing in one system. Rui Oliveira, IT Applications Manager at DS Smith Iberia says: “We expect to increase accuracy and reliability of our stock data for finished goods and wooden pallets, by minimizing errors in goods movements in the warehouse through automatic pallet reading, using RFID tags and image processing. We foresee substantial logistics efficiencies, as well as further future improvements based on the new technological capabilities and data made available with this project”.
Pure volume analysis of transport goods in the cloud offers significantly more possibilities today than it was previously possible on the shop floor, from productivity management, to process control, to better space utilization, and to tracking. As the DS Smith case illustrates, the close collaboration between SICK, Neadvance, and Microsoft demonstrates a system that offers far-reaching possibilities for more efficient logistics suitable for industry. Advanced freight dimensioning offers extensive opportunities to transport more efficiently. It also illustrates the importance of converting data into knowledge in order to improve value-added processes in manufacturing or logistics.
Following this successful pilot prototype implementation, international packaging manufacturer DS Smith believes that this new approach, with additional data made available through new technology, will help monitoring the material flow and optimize it in the long haul.
Read more
Faster in depalletizing: Robots see more with 3D snapshot technology
Monitor logistics data with Package Analytics to make informed decisions faster
Automated incoming goods inspection thanks to middleware and vertical integration