Met een productie van 110.000 sensoren, 520.000 ventielen en 5300 controllers per dag is het intern transport van goederen in de fabriek een hele uitdaging. Om dit efficiënter en ook kostenefficiënter te maken, werd in mei overgeschakeld op een geautomatiseerd transportsysteem waarbij zes AGV’s goederen van en naar de productielijnen brengen.
Voor het transport van bakjes met componenten werden speciale AGV’s ontwikkeld met daarop een platform met rollenbaantjes dat naadloos kan aansluiten op de rollenbanen die uit het magazijn komen en op de flowracks aan de productielijnen.
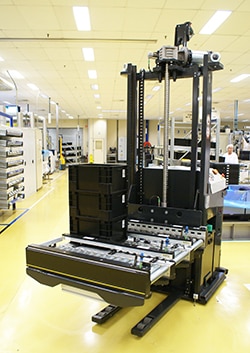
De transportorders voor dit systeem worden gegenereerd door een elektronisch kanbansysteem. Zodra in de productie een bakje uit een flowrack genomen wordt, krijgt men in het magazijn de opdracht om een nieuw bakje klaar te maken en aan de AGV mee te geven. Een sortersysteem tussen het magazijn en de productie groepeert de bakjes tot transportorders langs een bepaalde route. Op een accumulator naast elk flowrack worden de lege bakjes verzameld. Als een AGV plaats heeft op zijn platform en sensoren aangeven hoeveel lege bakjes klaar staan op een accumulator, kan de machine zelf beslissen om de lege bakjes mee terug te nemen naar het magazijn.
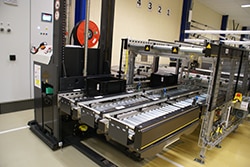
“Een dergelijk systeem werkt volledig autonoom en heeft in principe geen verdere feedback nodig”, legt Roel Hensmans uit. “Zodra de AGV ergens een pallet neerzet, weet de software dat zich op die positie een pallet bevindt. In de praktijk kunnen er echter allerlei redenen zijn voor de mensen in de productie om goederen te verplaatsen. Daarom wilden we een bijkomende detectie op elke palletpositie die aangeeft of er zich effectief een pallet bevindt. Op die manier kunnen we absoluut garanderen dat een AGV niet zal proberen om een pallet neer te zetten op een positie waar zich al een andere pallet bevindt.”
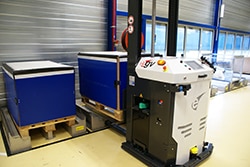
In de flowracks bestaat een gelijkaardige controle. Daar zijn het ultrasoonsensoren die vanop de AGV kunnen kijken of er plaats is in het kanaal van een flowrack alvorens er een bakje in te schuiven. Voor de palletposities bleek het logischer om op elke locatie een vaste sensor te plaatsen zodat het systeem op elk ogenblik ‘ziet’ welke posities ingenomen zijn.
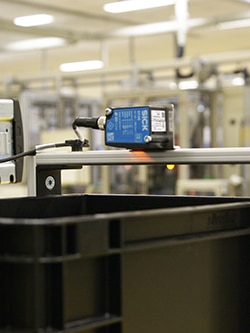
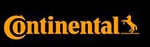
Continental Automotive Benelux bvba
Generaal de Wittelaan 5
2800 Mechelen
Tel : +32 15 28 96 40
https://www.conti-online.com
Peter.Van.Looy@continental-corporation.com