Depuis un an et demi, le fabricant de chocolats Natra Jacali à Bredene met le programme Overall Equipment Effectiveness en œuvre pour rendre sa production la plus rentable possible. Chaque interruption est enregistrée et analysée afin de générer des améliorations en continu. En fin de chaque ligne de production, des capteurs laser de SICK mesurent le rendement réel.
Combien de temps en pourcent ma production tourne-t-elle à pleine capacité? De nombreuses entreprises se posent cette question, et une fois qu’elles mesurent réellement leur OEE, le pourcentage est généralement plus bas qu’espéré. « La perception diffère souvent de la réalité », déclare Eric Cools, plant manager chez Natra Jacali à Bredene. « Des temps d’arrêt minimes, rapidement solutionnables et qui passent inaperçus, peuvent avoir un impact global important sur la disponibilité des machines. D’autre part, des problèmes très dérangeants pour les opérateurs semblent avoir un impact minimal par rapport à la réalité. »
L’OEE comme outil de gestion
Via l’Overall Equipment Effectiveness (OEE), on vise le produit de la disponibilité, les performances et la qualité d’une machine ou d’une ligne. La disponibilité est une partie du temps que la machine utilise effectivement. Les performances ont trait à la vitesse par rapport à la vitesse théoriquement réalisable. La qualité est la fraction des produits qui répondent dès la première fois aux spécifications souhaitées. Pour tous ces paramètres, Natra Jacali atteint un résultat OEE élevé de plus de 75% aux lignes soumises au programme depuis un an et demi.
Eric Cools: “Nous utilisons l’OEE comme un outil de gestion qui est suivi chaque jour. Chaque arrêt est enregistré dans un logiciel via lequel les opérateurs peuvent indiquer la raison et proposer des suggestions pour prévenir le problème. C’est devenu une forme de communication entre les opérateurs, le management et le service technique, et tout est mis en œuvre pour faciliter le travail des opérateurs. Les techniciens, grâce aux informations des opérateurs, ont une meilleure vision du fonctionnement des lignes, ce qui permet de prévoir des entretiens plus efficaces, d’apporter des améliorations, etc.”
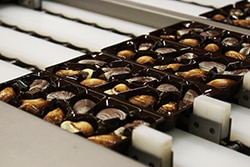
Natra Jacali est la filiale belge de Natra, le fabricant espagnol de chocolat. Elle a été fondée en 1988 par deux frères qui connurent un tel succès avec leurs fruits de mer en chocolat qu’ils ont dû passer à une production industrielle. Ces fruits de mer en chocolat, un produit typiquement belge, sont conçus pour offrir un produit adapté en été, qui est une basse saison pour les fabricants de chocolat. Depuis 2005, Jacali fait partie du groupe Natra lequel, en tant que représentant des vrais chocolats belges, a su acquérir une position solide.
La gamme des produits a été élargie au fil des ans et comprend, outre les fruits de mer, des barres de chocolat, des tablettes, des œufs de Pâques et des pralines. La majeure partie des produits est proposée sur le marché sous des labels privés, une activité où la rentabilité est essentielle. Voilà pourquoi l’entreprise accorde une grande attention à l’OEE.
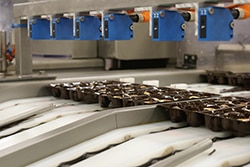
En première instance, Natra Jacali a implémenté un logiciel qui, à chaque takt de ligne, reçoit une impulsion de la machine de sorte que la production réelle puisse être tracée. A défaut d’impulsion, l’opérateur perçoit sur un écran tactile un aperçu des dérangements possibles où il peut indiquer le type de problème. Bien que cette méthode donne une image relativement précise de la disponibilité et des performances, celle-ci était néanmoins trop optimiste à propos de l’OEE réel.
«En fin de ligne, il y a à chaque fois huit trays côte à côte, remplis de fruits de mer », explique Eric Cools. « Pour avoir un système de traçabilité concluant à 100%, on ne voulait plus enregistrer le takt de machine mais le nombre réel de trays qui quittent la ligne. »
Pour réaliser cela, l’entreprise a fait appel à CDC Automatisatie, l’intégrateur spécialisé dans les solutions sur mesure en automatisation et technique d’entraînement.
« Au-dessus de la ligne, nous avons placé une rangée de cellules photoélectriques de SICK pour détecter les trays », raconte Christofe Decraene, administrateur de CDC Automatisatie. « Un PLC enregistre les signaux des cellules photoélectriques et les convertit en un train d’impulsions qui est dirigé vers le logiciel OEE. De cette manière, le logiciel peut compter les trays sans devoir adapter le système de traçabilité qui est un système fermé. »
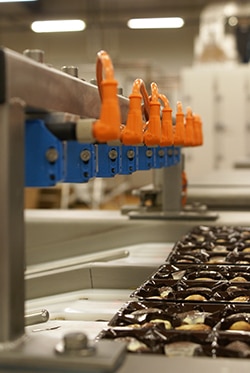
Une condition à cela était que la détection par les cellules photoélectriques soit fiable à 100%, ce qui n’était pas évident suite à la grande variété de couleurs et de matériaux des trays. Certains sont très foncés, d’autres brillent comme du métal ou ont presque la même couleur que le tapis convoyeur qui les transporte. Et s’il vient à manquer un tray, il y a toujours le guide qui doit pousser le tray et qu’il ne faut pas confondre avec le tray proprement dit.
La solution à tout cela a été trouvée avec la version ‘line’ des cellules photoélectriques WTB12 de SICK.
Christofe Decraene : « La cellule photoélectrique ne se limite pas à un petit point mais dessine une ligne de quelques centimètres de long dont la réflectance est détectée dans son ensemble. Ceci génère beaucoup plus de possibilités car la ligne est positionnée de manière telle qu’à chaque moment, non seulement le tray mais aussi plusieurs fruits de mer peuvent être détectés. Sur les chocolats, on a une réflexion claire et grâce à la ligne du capteur, cela donne une seule impulsion longue lorsqu’un tray passe, même si les chocolats sont à une certaine distance les uns des autres dans le tray. »
Le PLC combine les signaux de huit capteurs au-dessus de la ligne et perçoit, par takt, le nombre de trays qui se trouvent sur le convoyeur. Ce nombre est transmis dans un petit train d’impulsions au PC sur lequel tourne le logiciel OEE, au lieu de l’unique impulsion que le logiciel recevait jadis par takt. Après une légère adaptation au logiciel, celui-ci peut désormais compter le nombre réel de trays produits, et sur base du temps entre les petits trains d’impulsions, il dispose également d’un aperçu de la vitesse à laquelle la machine tourne. Un arrêt de ligne est également détecté car les cellules photoélectriques génèrent un signal anormalement long ou pas de signal du tout.
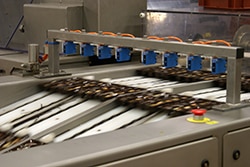
Cette adaptation montre toute son utilité car le logiciel perçoit chaque tray manquant en fin de ligne. L’opérateur reçoit, comme lors des arrêts de la machine, un signal et peut en indiquer la raison sur son écran tactile. Sur base de cela, on peut étudier les adaptations qu’il y a lieu de faire pour éviter ce problème dans l’avenir. Cette approche systématique est appliquée depuis plus d’un an chez Natra Jacali et porte ses fruits car l’OEE a sensiblement augmenté durant cette période, jusqu’à plus de 80%. Et quand on parle d’OEE chez Natra Jacali, cela signifie aussi une comparaison avec le maximum absolu pouvant être atteint sans enjoliver les faits par rapport à la réalité, car chaque tray qui n’est pas produit est détecté en fin de ligne par les capteurs.
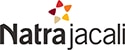
Natra Jacali
Brugsesteenweg 95
8450 Bredene
Belgique
Tél. +32 (0)59 34 03 30
http://www.natra.be
Eric.cools@natra.com
CDC Automatisatie
Meensesteenweg 542
8800 Rumbeke – Roeselare
Belgique
Tél. +32 (0)476 25 43 63
http://www.cdcautomatisatie.be/
christofe.de.craene@cdcautomatisatie.be