Ein Freitagvormittag Mitte Januar 2024 in der großen Montagehalle der Maschinenbaufirma Karl Eugen Fischer GmbH in Burgkunstadt in Oberfranken: Der weltweit führende Hersteller von Cordschneideanlagen für die Reifenherstellung wird heute, rund eine Woche vor der Auslieferung an den Kunden, eine solche Anlage auf Herz und Nieren prüfen – und wir dürfen live dabei sein, um in Text, Bild und Video darüber zu berichten. Es handelt sich dabei nämlich um eine besondere Maschine, die dank des Einbaus einer Lösung von SICK die Performance dieser Anlagen auf ein neues Level hebt.
MLG-2 WebChecker von SICK hebt Cordschneideanlagen in der Reifenherstellung auf ein neues Level
Auch Achim Sorg, Lead Account Manager Automotive & Electronics SICK Vertriebs GmbH und Jörg Weiser, Application Engineer Automotive & Electronic SICK Vertriebs GmbH, sind heute zu ihrem Kunden KE Fischer gekommen: Die beiden Vertriebsfachleute von SICK hatten die Idee, die SICK-Lösung für diese Art der Anlagen zu nutzen. Gemeinsam mit Frank Schmidt, Head of Software, Electric Engineering & R&D bei KE Fischer, und seinem Team haben sie das Vorhaben in die Tat umgesetzt.
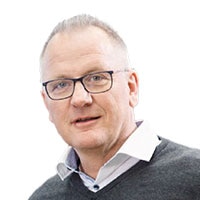
Auch Reifen haben Gürtel
Unser Weg führt uns durch die riesige Halle zur funkelnagelneuen, frisch lackierten, rund 40 Meter langen Cordschneidemaschine, die bereits im Testbetrieb läuft und von mehreren Mitarbeitenden von KE Fischer mit Argusaugen überwacht wird. Es riecht nach Metall und Reifengummi.
Zunächst erklärt uns Frank Schmidt, was hier eigentlich passiert: Die Anlage schneidet sogenanntes kalandriertes Stahlcordmaterial. Das sind gummibeschichtete Stahldrähte, die für den sogenannten „Gürtel“ im Reifen gebraucht werden. In die Anlage wird Stahlcordmaterial von einer mehrere Meter langen Rolle eingeführt. Ein riesiges Messer schneidet nun das im Winkel zugeführte Material in einzelne Streifen ab. Der Zuschnittswinkel kann verändert werden, indem die Komponente der Zuführung der Stahlcordbahn auf im Boden eingelassenen Schienen rezeptabhängig halbautomatisch verfahren wird.
Diese im Winkel zugeschnittenen Streifen fügt die Anlage nun wieder zu einem Endlosband zusammen und slittert dieses dann noch einmal in zwei Einzelstreifen. So entstehen am Ende mehrere neue Spulen Stahlcordmaterial, in dem die Stahldrähte schräg verlaufen. Das sei für die Stabilität der Reifen erforderlich, erklärt uns Frank Schmidt: „Für den nächsten Verarbeitungsschritt in der Reifenherstellung werden mehrere Materiallagen mit Stahl- und Textilcord zusammengesetzt. Für die Cordschneidemaschine heißt das, dass sie diese Streifen so präzise wie möglich vorbereiten muss – eine besonders genaue und leistungsstarke Kantenführungslösung und Inline-Qualitätsüberwachung des Materials ist also das A und O.“
Perspektive in Richtung Digitalisierung
Und wo genau ist nun die Innovation, die in dieser Anlage verbaut ist? Dazu muss Frank Schmidt etwas ausholen: Bisher waren in derartigen Anlagen zur Breitenmessung des Materials sowie der korrekten Führung in einer bestimmten Spur standardmäßig Lösungen mit einer CCD-Zeilenkamera in Verbindung mit einem Aktuator, einem Regler und weiteren Komponenten üblich. Das hatte einige Nachteile: „Diese Lösungen müssen aufwendig eingestellt werden, damit alle zu produzierenden Materialbreiten auf der Anlage verarbeitet werden können“, erklärt Frank Schmidt. Dazu kommt: Sie sind sehr wartungsintensiv, und die Anwender können sie in der Regel nicht selbst reparieren. Müssen sie ausgetauscht werden, dann steht die Anlage still, weil die neue Kamera erst aufwendig parametriert und kalibriert werden muss.
Die Idee, diese unpraktische „Blackbox“-Lösung durch den MLG-2 WebChecker von SICK zu ersetzen, hatte Achim Sorg im Jahr 2020. Das Automatisierungslichtgitter nutzt mehrere in regelmäßigen Abständen angeordnete Lichtschranken zur genauen Bahnenvermessung. „Dieser Schritt ist ein Paradebeispiel dafür, wie wir bei SICK auch Lösungen an unsere Kunden herantragen, die diese vielleicht noch gar nicht auf dem Schirm hatten“, sagt Achim Sorg. Er und Jörg Weiser, der über langjährige Erfahrung in der Reifenindustrie verfügt, arbeiteten den Vorschlag aus – und rannten bei Frank Schmidt damit offene Türen ein: Dieser hatte schon lange beobachtet, dass die Zeilenkamera-Lösung anfällig und wartungsaufwendig war. „Die Lösung ist einfach nicht mehr zeitgemäß – und bot auch keine Perspektive in Richtung Digitalisierung“, sagt er. „Das wollte ich gerne ändern, und der MLG-2 WebChecker war dafür prädestiniert.“
SICK und KE Fischer starteten ein Pilotprojekt, um die Umsetzbarkeit des Vorhabens zu prüfen – mit positivem Resultat: 2021 stattete KE Fischer als weltweit erster Hersteller von Stahlcordanlagen seine Anlagen erstmals mit dem MLG-2 WebChecker aus – zunächst an einer Stelle in der Anlage, dann an immer mehreren. „Wir haben den MLG-2 WebChecker anfangs sogar auf eigene Kosten in Anlagen eingebaut, um unseren Kunden die Möglichkeit zu geben, die Lösung auszuprobieren und sich erst dafür zu entscheiden, wenn sie überzeugt sind“, blickt Frank Schmidt zurück. Auch seitens SICK wurde der MLG-2 WebChecker noch mal auf die speziellen Bedürfnisse von KE Fischer hin angepasst. Das Engagement hat sich gelohnt: Heute laufen schon über 20 Anlagen mit MLG-2 WebChecker bei den Kunden des Maschinenbauers.
Perfektes Qualitätsmanagement-Tool
In der Anlage, die wir heute sehen, sind insgesamt sieben MLG-2 WebChecker verbaut. Frank Schmidt zeigt sie uns über die ganze Länge der Anlage hinweg. Die Geräte messen kontinuierlich die Breite der Stahlcordbahn und kontrollieren auf den Zehntelmillimeter genau, ob die Toleranzen eingehalten werden. Ist das einmal nicht der Fall, so reguliert die Anlage autonom innerhalb eines gewissen Toleranzbereichs per Servo nach, bis die Breite passt.
„Das ist das perfekte Qualitätsmanagement-Tool über den gesamten Produktionsvorgang hinweg“, erklärt Frank Schmidt. Dabei ist das System sehr vielseitig: Der MLG-2 WebChecker kann Bahnen zwischen 145 mm und 3.150 mm messen. Die flexible Bahnbreitenmessung macht den Formatwechsel denkbar einfach – ohne Stillstand der Anlage.
Um uns das zu zeigen, variieren die Mitarbeiter die Breite der Streifen, die von der Rolle abgeschnitten werden. „Egal ob die Bahn mittig geführt wird oder versetzt, egal ob eine oder zwei Bahnen nebeneinander auf der Anlage laufen – man kann den MLG-2 WebChecker für all das einstellen. Er kann sogar bis zu fünf Bahnen gleichzeitig vermessen“, sagt Frank Schmidt.
„Auch der Aufwand für die Instandhaltung ist deutlich geringer als bei der alten Lösung. All das erhöht die Maschinenverfügbarkeit und damit letztendlich die Produktivität der Anlage.“ Und noch einen wesentlichen Vorteil hat der WebChecker: Weil die Anlage deutlich genauer produziert, wird Ausschuss durch falsch zugeschnittene Bahnen reduziert – ein großes Plus für die Umwelt.
Für Frank Schmidt ist der MLG-2 WebChecker jedoch vor allem auch im Hinblick auf die Digitalisierung ein wichtiger Schritt: Aus den Daten, die das Lichtgitter generiert, lassen sich wertvolle Erkenntnisse gewinnen. Die Open-Source-Grundlage und grundsätzliche Softwarebausteine liefert SICK, individuelle Bausteine konkret für diese Anwendung hat KE Fischer selbst entwickelt: „Unsere Algorithmen werten die Daten intelligent aus und erstellen Analysen, die dem Bediener, Wartungs-oder Qualitätspersonal in Echtzeit zur Verfügung stehen“, sagt Frank Schmidt.
Auf einem Tablet zeigt er uns, wie das aussieht. „Diese Daten liefern zum Beispiel Erkenntnisse zur Wartung und Qualität: Wo gibt es Probleme, wo können wir optimieren? Wie ist die Qualität der Bahn – aus dem vorgelagerten Produktionsprozess wie auch hier in dieser Anlage? Wir machen mit unserer Lösung unsichtbare Daten sichtbar. Das ist ein klarer Mehrwert für den Kunden.“
Generell verfolgt KE Fischer das Ziel, die Anlagen für den Bediener so einfach wie nur möglich zu machen: „‚Hands off, eyes off‘ im Sinne einer autonomen Maschine ist die Devise. Dem sind wir mit dem WebChecker auch einen großen Schritt nähergekommen“, sagt Frank Schmidt.
Die drei Herren sind sich einig: Der MLG-2 Webchecker hat das Potenzial, eine neue Trendlösung für die Kantenführung und als Messsystem in der Reifenherstellung zu werden. „Dem hat Frank Schmidt den Weg geebnet“, sagt Achim Sorg. Bei der Zusammenarbeit haben beide Parteien viel dazu beigetragen, die Lösung immer weiter zu verbessern. Und so lobt auch Frank Schmidt die Kundenbetreuung von SICK: „Hier hebt sich SICK stark vom Wettbewerb ab. Achim und Jörg hatten immer ein offenes Ohr und sind auf alle unsere Anforderungen und Wünsche eingegangen – so lange, bis die Lösung gepasst hat.“
Inzwischen ist es Nachmittag geworden, die Montagehalle hat sich geleert. Der Testlauf wird für heute beendet, und auch wir haben alles „im Kasten“. In der kommenden Woche werden Frank Schmidt und sein Team noch ein paar Kleinigkeiten optimieren. Dann macht sich die Anlage auf den Weg zum Kunden – um dort alle ihre Vorteile voll auszuspielen.
Karl Eugen Fischer GmbH
Die Karl Eugen Fischer GmbH (KE Fischer) ist Weltmarktführer für Stahl- und Textilcordschneideanlagen, die zur Herstellung von Zweirad-, PKW-, SUV-, LKW- und Offroad-Reifen benötigt werden. Hauptsitz und Produktionsstätte des 1940 gegründeten Unternehmens ist Burgkunstadt. Tochtergesellschaften gibt es in den USA, in China und durch die Übernahme von Konštrukta TireTech (KTT), einem Hersteller von Extrusions- und Schneidanlagen für die Reifenindustrie, seit Dezember 2022 auch in der Slowakei. Insgesamt beschäftigt das Unternehmen rund 600 Mitarbeitende. Innerhalb der vergangenen 50 Jahre lieferte KE Fischer über 900 Schneideanlagen an Kunden in rund 50 Länder weltweit.Pace: Magazin zum Geschäftsbericht 2023
Die hohe Dynamik in den Märkten erfordert und der technologische Fortschritt ermöglicht beschleunigte Lösungsfindungen. Wir passen immer wieder unser Tempo an, um einen Vorsprung zu gewinnen und zu halten, indem wir unsere Beschleunigungskräfte sinnvoll einsetzen.
Die Beiträge im Magazin zeigen: Wer sich durch Schnelligkeit Vorsprung und Zeit verschafft, kann diese intelligent für neue Ideen und nachhaltige Entscheidungen nutzen.
Lesen Sie auch die anderen Artikel aus unserem Geschäftsbericht 2023